Imagine a world without electricity. No lights, no appliances, no internet. It’s hard to fathom, isn’t it? Yet, for all the convenience it brings, electricity can be a powerful force, capable of immense energy. And to harness that energy for industrial and commercial applications, we rely on a crucial component: the motor starter. But understanding how to wire it, especially for a 3-phase system, can seem like a daunting task. Fear not! This article will take you on a journey through the intricate workings of the 3-phase motor starter wiring diagram, demystifying the process and empowering you to control the power of electricity safely and efficiently.
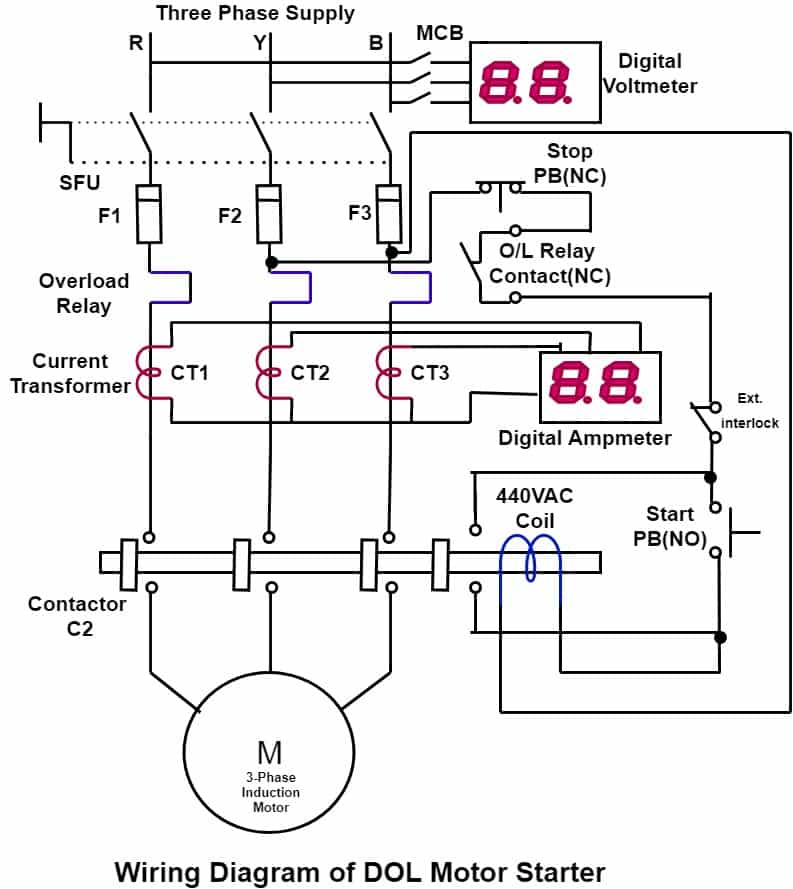
Image: wiringengineabt.z19.web.core.windows.net
The heart of any industrial operation often lies within the rhythmic hum of motors, driving machinery and powering production. But these powerful machines need more than a simple switch to activate them. Enter the motor starter, a crucial device designed to protect the motor, control its operation, and provide a safe and user-friendly interface. While there are various types, today we’ll delve into the world of 3-phase motor starters, the backbone of many industrial installations. A 3-phase motor starter is essentially a control system that allows you to safely start, stop, and protect your 3-phase motor. This is essential for applications ranging from large-scale factories to even smaller businesses with automated processes.
Fundamentals of a 3-Phase Motor Starter
Before diving into the wiring diagram, it’s essential to understand the building blocks of a 3-phase motor starter. The core components are:
- Contactors: These are electromagnetic switches that open and close the circuit to start and stop the motor.
- Overload Relays: These devices guard against excess current, preventing damage to the motor during overload conditions. You’ll often see a thermal overload relay used here.
- Control Circuit: This part of the system is responsible for controlling the contactor and overload relay. It typically involves push buttons, selector switches, and other control devices.
- Auxiliary Components: These may include fuses, circuit breakers, and other safety devices, all working together to ensure a safe and reliable motor operation.
Deciphering the Wiring Diagram
Now let’s delve into the wiring diagram itself. It might look like a confusing maze of lines and symbols at first, but with a methodical approach, it becomes clear.
- Power Supply: The first step is understanding the power source. For a 3-phase system, you’ll typically see three lines representing the phases (usually labeled as L1, L2, and L3). These lines carry the electric current that powers the motor.
- Motor Terminals: Next, you’ll see the motor itself. The motor terminals, usually three in number (T1, T2, and T3), connect directly to the contactor’s main contacts.
- Contactor: The contactor is the heart of the motor starter. It has two sets of contacts:
- Main Contacts: These are the ones that directly connect the motor to the power supply when the contactor is energized.
- Auxiliary Contacts: These are used for various control functions, such as interlocking and signaling.
- Overload Relay: The overload relay is wired in series with the motor. It protects the motor by monitoring current. If the current exceeds a predetermined threshold, the overload relay will open the circuit, interrupting the flow of current to the motor.
- Control Circuit: The control circuit is responsible for operating the contactor and the overload relay. It’s typically wired with push buttons, limit switches, and other control devices. The control circuit is often wired with a separate, lower voltage to ensure worker safety. This is usually called a “pilot circuit” or a “control circuit.”
Let’s visualize this: A simple 3-phase motor starter wiring diagram might show L1, L2, and L3 going through a fuse or circuit breaker, then to the main contacts of a contactor. The main contacts are connected to the motor terminals T1, T2, and T3. The overload relay is connected in series with the motor, and the control circuit will likely be shown with a separate set of lines going to push buttons (Start and Stop), a selector switch for motor direction (if applicable), and possibly other control devices.
Understanding the Control Logic
The control circuit uses logic to determine whether the motor should be on or off. This logic can be simple or quite complex, depending on the application. Here are some common examples:
- Direct-on-Line (DOL) Starting: This is the simplest method. When the start button is pressed, the contactor energizes, directly connecting the motor to the power supply. Pressing the stop button de-energizes the contactor, interrupting the current to the motor.
- Star-Delta Starting: This method is used for larger motors. The motor is initially connected in a star configuration (where the phases are connected to the motor in a Y-shape), and then, once the motor reaches a certain speed, it’s switched to a delta configuration (where the phases are connected to the motor in a triangle). This allows the motor to start with lower current, reducing stress on the electrical system.
- Reduced Voltage Starting: This technique uses various methods to initially reduce the voltage supplied to the motor, limiting starting current and reducing stress on the system.
![[DIAGRAM] 3 Phase Starter Diagram - MYDIAGRAM.ONLINE](https://1.bp.blogspot.com/-0alMfRDkpT0/WdCyu1JEyII/AAAAAAAABO8/m_3Ekgb0ImE-e0-3mUuszcI9GOLbyERAACLcBGAs/s1600/direct%2Bonline%2Bstarter%2Banimation%2Bpart%2B4.gif)
Image: mydiagram.online
Safety First!
It’s crucial to emphasize the importance of safety when working with electrical systems. Never attempt to work on electrical equipment without proper training and authorization. Always disconnect the power supply before working on any electrical wiring. If you are unsure about anything, consult with a qualified electrician.
Beyond the Basics
The world of motor starter wiring diagrams extends beyond the fundamentals. There are advanced applications, such as:
- Variable Frequency Drives (VFDs): These provide precise motor speed control, increasing energy efficiency and productivity.
- Soft Starters: These gradually increase voltage to the motor, minimizing starting current inrush.
- Motor Protection Relays: These monitor motor parameters beyond just overload, such as temperature and ground faults, providing comprehensive protection.
Expert Advice: Making it Work for You
To truly master the art of motor starter wiring, it’s helpful to seek advice from experts. An electrician specializing in industrial control systems can guide you through specific applications and provide insights on best practices. Resources such as electrical code manuals, online forums, and manufacturer documentation are also invaluable.
Wiring Diagram For Motor Starter 3 Phase
https://youtube.com/watch?v=hOS3R8GPvCw
A Powerful Tool for Your Success
Understanding the 3-phase motor starter wiring diagram is not just about technical knowledge; it’s about gaining control over a powerful tool that can drive your operations, from factories to smaller businesses. The journey may seem complex at first, but with patience and practice, the intricate network of wires and components will become clear. So, take the time to learn, seek guidance, and practice. The reward? A mastery of the power that flows through your circuits, and a sense of accomplishment knowing you’ve expanded your knowledge to navigate the world of electricity and its applications.