Have you ever stared at a Lincoln 225 arc welder wiring diagram and felt a wave of confusion wash over you? The intricate network of wires, terminals, and components can seem daunting, even for seasoned welders. But fear not! This guide will unravel the complexities of the Lincoln 225 wiring, empowering you to understand the flow of electricity and safely operate your powerful welding tool.
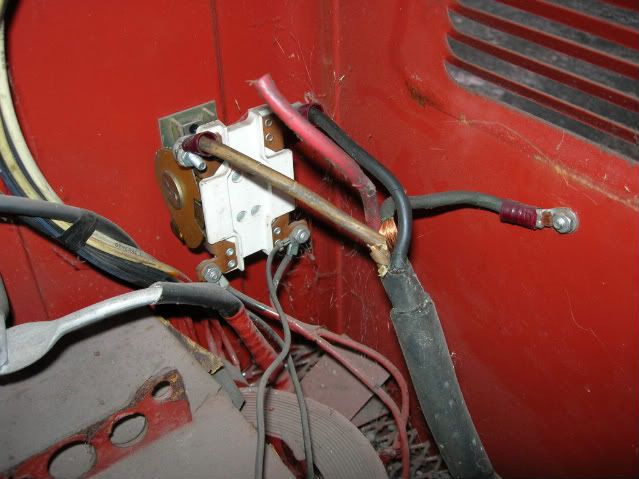
Image: mydiagram.online
The Lincoln 225 is a workhorse in the welding world, known for its reliability and versatility. Understanding the wiring diagram is crucial for troubleshooting potential problems, performing maintenance, and maximizing the welder’s performance. Whether you’re a beginner or a seasoned professional, this guide will provide you with the knowledge to confidently navigate the intricate connections within your Lincoln 225.
Unveiling the Wiring Diagram: A Journey Through the Circuitry
The Lincoln 225 wiring diagram is a visual map of the electrical pathway within the welder. It showcases the intricate network of wires and components that work in synergy to generate the intense heat needed for welding. The diagram is typically printed on a sticky paper sheet and is often found inside the welder’s lid, providing a handy reference during usage and troubleshooting.
Key Components: Understanding the Power Players
Before diving into the detailed wiring, let’s familiarize ourselves with the key components involved in the Lincoln 225’s electric symphony:
- Power Supply: This is the heart of the welder, converting household power into a high-voltage, high-amperage current. It is typically a transformer, which uses electromagnetic induction to step up the voltage.
- Control Panel: This panel houses the switches, knobs, and gauges that allow you to control the welding parameters, such as amperage, voltage, and arc length.
- Electrode Holder: This device holds the welding electrode, channeling the current to the arc.
- Work Clamp: This clamp connects to the workpiece, closing the electrical circuit and allowing current to flow through the weld pool.
- Ground Wire: This wire connects the work clamp to the ground terminal on the welder, completing the electrical path and ensuring safe operation.
Tracing the Electrical Flow: A Step-by-Step Guide
- Power Entry: The electrical journey begins at the power cord, which carries the incoming current from your wall outlet. This cord is typically rated for 220 volts, although some models may require higher voltage.
- Power Supply: The power cord is connected to the power supply transformer, which is responsible for stepping up the voltage to a much higher level. The transformer uses electromagnetic induction to transfer energy between windings.
- Control Panel: The power supply then delivers the electricity to the control panel. The panel houses switches, dials, and gauges that allow you to adjust the welding amperage and voltage based on your specific welding requirements.
- Electrode Holder: The chosen amperage setting is processed through various circuits and ultimately delivered to the electrode holder. This component serves as the conduit for the welding current, transferring it to the electrode.
- Arc Initiation: When the electrode touches the workpiece, the circuit completes, creating an arc. This arc is a continuous flow of electricity between the electrode and the workpiece.
- Work Clamp: The work clamp, connected to the workpiece, completes the electrical circuit, allowing the current to flow freely. This completes the electrifying dance that allows the arc to melt the metal and create a strong weld.
- Ground Wire: The ground wire, connected to both the work clamp and the welder’s ground terminal, acts as a safety measure. It provides a low-resistance path for the current to flow back to the welder in case of an accidental ground fault.

Image: www.pinterest.com
Decoding the Wiring Diagram: A Graphical Language of Power
The Lincoln 225 wiring diagram is a key to understanding the welder’s intricate electrical systems. Here’s a breakdown of its elements:
- Lines: Solid lines represent electrical conductors (wires), while dashed lines usually indicate control signals.
- Symbols: Each symbol represents a specific component within the welder, such as switches, resistors, capacitors, and transformers. Each symbol is standardized to ensure universal understanding.
- Terminals: Each component has terminals that are numbered or lettered, indicating the connection points for wires.
- Colors: Different colors may be used for wires to indicate specific functions. For example, black usually represents the live wire, white the neutral, and green or yellow the ground.
Practical Applications: Understanding the Wiring’s Impact
Understanding the Lincoln 225 wiring diagram has several practical applications that go beyond simply deciphering the electrical circuit:
- Troubleshooting: If your Lincoln 225 is experiencing problems, the wiring diagram can help you pinpoint the fault. By tracing the electrical pathway, you can identify potential issues, such as broken or loose connections, faulty components, or improper wiring.
- Maintenance: The diagram helps you perform routine maintenance, such as cleaning terminal connections, checking for loose wires, or replacing worn-out components.
- Upgrades: The wiring diagram can be referenced when modifying or upgrading your welder, ensuring that you connect components correctly and maintain the integrity of the electrical system.
- Safety: Understanding the wiring diagram is essential for safe operation. By knowing the path of the current, you can avoid potential hazards and ensure that the welder is properly grounded.
Lincoln 225 Arc Welder Wiring Diagram
Mastering the Lincoln 225: Embracing the Power of Knowledge
Conquering the Lincoln 225 wiring diagram is an important step in mastering your welding skills. It allows you to troubleshoot issues, perform preventative maintenance, and optimize the welder’s performance for your specific projects. The next time you encounter a welding challenge, remember to refer to the wiring diagram as your trusted guide.
Keep in mind that working with high-voltage electricity can be dangerous. Always disconnect the welder from the power source before performing any maintenance or troubleshooting. If you’re unsure about any aspect of the wiring diagram or have any concerns, consult a qualified electrician or welding professional.
With a deeper understanding of the Lincoln 225 wiring diagram, you are equipped to unlock the full potential of this powerful welding tool, enhancing your welding expertise and achieving impressive results. Let the flow of electricity guide your creativity and enhance your welding journey!